Монтаж GaN- и GaAs-кристаллов при производстве радиоэлектронных модулей
Современные изделия СВЧ-электроники на базе интегральных схем из GaAs и GaN имеют более высокую энергоэффективность и обеспечивают большую мощность, чем предыдущие поколения твердотельных приборов. Устройства нового поколения требуют повышенной точности, согласованности и прослеживаемости на протяжении всего цикла сборки для обеспечения эффективного теплоотвода от термонагруженной области затвора транзистора. Уникальные свойства новых приборов диктуют повышенные требования к технологическому процессу — и технологам приходиться решать множество проблем, связанных с качеством и толщиной металлизации, определением методики монтажа, предотвращением загрязнений и соблюдением условий хранения, качеством вакуумных захватов, входным и выходным контролем.
Рассмотрим ключевые факторы, определяющие процесс монтажа кристаллов при сборке СВЧ-электроники, применяемой при производстве радиоэлектронной аппаратуры специального назначения, а также в аэрокосмической, спутниковой и телекоммуникационной отраслях.
Илья Корочкин — Глобал Микроэлектроника, Россия
В России, как и за рубежом, технологии создания изделий СВЧ электроники отнесены к критическим, без развития которых невозможно создание высокотехнологичной конечной продукции для различных отраслей, а также современных и перспективных образцов вооружений и военной техники.
Изделия СВЧ электроники включают широкий спектр различных классов и групп приборов, отличающихся по назначению, физическому принципу действия, конструкции и технологии изготовления. Как за рубежом, так и в России в последние десятилетия особенно бурное развитие получила твердотельная СВЧ электроника и, в первую очередь, ГИС и МИС, предназначенные для использования в различных диапазонах СВЧ.
В то время как радиочастотные, микроволновые и миллиметровые технологии предыдущих поколений строились на дискретных компонентах и ламповых усилителях бегущей волны, современная промышленность практически повсеместно перешла на твердотельные технологии (транзисторы и МИСы на основе GaAs и GaN полупроводников). Внедрение новой компонентной базы было технически и экономически необходимо для достижения критически важных характеристик в современных фазированных антенных решётках (АФАР) и сложных технологиях модуляции сигнала, обеспечивающих низкую вероятность перехвата и обнаружения радаров с электронным сканированием луча, а также повышением коммуникационных возможностей в условиях вновь разворачивающихся театров военных действий.
Основные материалы, используемые сегодня для чипов интегральных схем СВЧ — кремний (для низкочастотных), арсенид галлия (для высокочастотных), нитрид галлия (для МИС миллиметрового диапазона). При этом в количественном соотношении наиболее массовыми являются СВЧ приборы на основе арсенида галлия. Ещё совсем недавно доля их на мировом рынке составляла до 80%.
Транзисторы на основе нитрида галлия, созданные впервые в 1993 году, существенно расширили возможности приборов СВЧ-диапазона. Эти приборы способны работать в значительно более широком диапазоне частот и при более высоких температурах, а также с большей выходной мощностью по сравнению с приборами на Si, GaAs, SiC или любом другом серийно освоенном материале.
Номенклатура выпускаемых GaN усилительных МИС пока в десятки раз меньше, чем GaAs МИС, однако, фаза промышленного освоения этой технологии в России только началась и в ближайшие годы рынок будет резко расширяться. Проблемными моментами, сдерживающими развитие GaN-приборов, среди прочих, являются необходимость выращивания эпитаксиальных структур GaN на чужеродных (отличающихся по параметрам кристаллической решётки, тепловому расширению и т.д.) подложках и задача обеспечения адекватного теплоотвода от активной структуры.
GaN и GaAs транзисторы и МИСы входят в состав наиболее критичных устройств — приёмников и передатчиков современных средств радио- и спутниковой связи, радиолокационных приёмо-передающих модулей и работают на суше, море, воздухе и космосе. Несмотря на то, что твердотельные компоненты рассчитаны на работу в условиях повышенных нагрузок и имеют длительный ресурс, крайне важно тщательно соблюдать требования к работе с ними.
Даже небольшое загрязнение, несоблюдение правил обращения с кристаллами или отклонения от технологического процесса сборки могут существенно снизить срок службы или паспортные выходные параметры, что критически важно при обеспечении стабильной широкополосной связи в СВЧ-диапазоне. Вот почему строгое соблюдение технологического процесса сборки и обращения с кристаллами становится для инженера-монтажника не менее важным, чем правильный расчёт усилителя мощности для инженера-разработчика. Один из ключевых этапов сборки таких модулей — процесс монтажа GaN и GaAs кристаллов при котором выполняется механическая фиксация компонента на носителе (подложке, теплоотводе, пьедестале) с обязательным обеспечением надёжного электрического и термического контакта. |
![]() Рис. 1 — кристалл GaAs, смонтированный на LTCC основание |
Основные методы монтажа кристаллов
Чтобы гарантировать, что сборка представляет собой механически надёжную и термически/электрически эффективную систему, соединение между кристаллом и подложкой должно удовлетворять следующим требованиям:
- обладать достаточной адгезией
- иметь высокую теплопроводность для обеспечения теплоотвода от кристалла
- обеспечивать низкое удельное электрическое сопротивление для минимизации потерь на проводимость
- иметь согласованный коэффициент термического расширения (далее — КТР) между подложкой и кристаллом
- сохранять стабильные показатели при рабочей температуре на протяжении всего жизненного цикла изделия
Смонтировать мощный GaN или GaAs кристалл с выполнения таких требования можно тремя различными методами:
- вакуумная пайка на эвтектику
- монтаж с притиркой
- монтаж на адгезив
каждый из которых имеет свои преимущества и недостатки. Выбор, в конечном счёте всегда предстоит сделать команде технологов и разработчиков исходя из требований, предъявляемых к изделию, и учитывая три основных ограничительных фактора:
- стоимость
- теплопроводность
- согласование КТР
Далее в статье приводится обоснование применения каждого из этих методов.
Монтаж кристалла на эвтектику
Пайка — наиболее распространённый метод монтажа GaN и GaAs МИС, обеспечивающий неразъёмное соединение. Спаиваемые поверхности и припой приводятся в соприкосновение и подвергаются нагреву до температуры плавления припоя (определяемой его составом), но ниже температуры плавления металлизации. В результате припой переходит в жидкое состояние и смачивает поверхности. Нагрев прекращается, и припой переходит в твёрдую фазу, образуя соединение. Благодаря своим металлическим свойствам, такое соединение обеспечивает оптимальные электрическую, термическую и механическую связи между соединяемыми поверхностями.
Подавляющее большинство компонентов, участвующих в процессе монтажа GaN GaAs МИС, — кристаллы, подложки, теплоотводы — имеют золотую металлизацию. Этим обоснован и выбор основного материала припоя для пайки данных компонентов — взаимодействие золота с золотом обеспечивает наиболее качественную и надёжную связь. В качестве вспомогательного материала используется олово, а композицию сплава (то есть соотношение массовых долей веществ) определила его точка эвтектики. Эвтектическая композиция представляет собой жидкий раствор, кристаллизующийся при наиболее низкой температуре для сплавов данной системы. Соответственно, температура плавления сплава эвтектического состава — также самая низкая, по сравнению со сплавами другого состава для данной системы компонентов. Таким образом, эвтектическая композиция AuSn в соотношении 80/20% по массовой доле стала самым распространённым сплавом для монтажа кристаллов.
Эвтектика золото-олово отлично сочетается с золотой металлизацией кристаллов и подложек и демонстрирует высочайшую стабильность и надёжность на протяжении всего жизненного цикла.
Сплав AuSn изготавливается в виде твёрдой ленты, обычно толщиной от 15 до 50 мкм, из которой вырубаются отдельные кусочки фольги (преформы) в зависимости от размера кристалла. Такой форм фактор позволяет точно контролировать объем припоя, состав и состояние поверхности и, как следствие, обеспечивать широкое технологическое окно процесса оплавления, надлежащее качество и стабильность паяного соединения определяя, тем самым, качество готового изделия и позволяя оценивать такую характеристику процесса как Cpk.
Забегая вперёд, стоит отметить, что в последнее время многие серийные производители пытаются уйти от использования преформ в пользу более технологичного метода — прямого нанесения припоя напылением на обратную сторону кристалла непосредственно в процессе его изготовления на полупроводниковой фабрике. Такой подход обеспечивает максимальную чистоту и толщину припоя, позволяет уйти от использования преформ существенно упрощая процесс сборки. Однако, процесс напыления — сложный технологический шаг, который требует внесения изменений в утверждённую технологию производителя кристаллов, что на практике бывает непросто сделать. В данной статье рассматривается «классическая» технология монтажа с использованием преформ, хотя описанные в ней принципы справедливы и для монтажа с напылённым припоем.
Вернёмся к рассмотрению физических свойств соединения. Различие в КТР используемых материалов обуславливают возникновение термических напряжений в кристалле, как в процессе сборки, так и в процессе эксплуатации, особенно при термоциклических воздействиях, поэтому согласование КТР компонентов соединения (преформы, кристалла, подложки) особенно важно для повышения надёжности сборки. Поскольку преформа AuSn — это твёрдый припой, а GaAs — очень хрупкий материал, необходимо подбирать материал подложки так, чтобы его КТР соответствовал КТР GaAs (Таблица № 1). Несмотря на то, что GaN на SiC более устойчив, чем GaAs, вопрос согласования КТР при проектировании этих изделий также открыт. Приемлемым диапазон КТР для материалов подложки под GaAs составляет от 6 до 10 10-6/К-1 — в него попадают алюмооксидная керамика Al2O3, Cu-W, Cu-Mo и сплав Fe-Ni. Материалы с КТР ниже, чем у GaAs, такие как ковар или алюмонитридная керамика AlN не должны использоваться из-за возможности образования термомеханических напряжений во время сборки или эксплуатации. Базовые материалы, которые подходят для GaAs, могут быть использованы для устройств GaN без ограничений, но для материалов с более широким диапазоном значений КТР рекомендуется проводить тщательный анализа прочности соединения и устойчивости к термоциклированию во всем допустимом температурном диапазоне, так как отказы могут возникнуть только при экстремальных рабочих температурах.
Материал | Теплопроводность, Вт/мК | КТР, 10-6/К-1 |
Керамика Al2O3 | 20 | 8,2 |
GaAs | 56 | 5,9 |
GaN | 130 | 4 |
Mo | 138 | 5,1 |
Керамика AlN | 170 | 4,0–6,0 |
Cu15W85 | 185 | 7,8 |
Cu40Mo60 | 230 | 9.1 |
SiC | 240 | 2,5 |
CPC (1:1:1) | 260 | 9,5 |
CMC (2:1:2) | 285 | 10 |
Cu | 390 | 17 |
Синт. алмаз | 1000 | 1 |
Однако, теоретический расчёт устойчивости к термоциклированию может быть подтверждён на практике только при обеспечении близкого к расчётному значения теплоотвода от кристалла через паяное соединение. Основная проблема при пайке кристаллов — это неоднородности в эвтектическом слое под кристаллом (несплошности эвтектики, микротрещины и т. п.), образованные в результате газовыделений или попадания загрязнений. Проблему нельзя недооценивать — зарубежные производители потратили десятки лет, чтобы добиться приемлемого качества паяного соединения.
Формирование неоднородностей приводит к изменению тепло-электрического состояния изделия. Скорость деградационных процессов экспоненциально возрастает при увеличении температуры и локализуется в областях микронеоднородностей в следствие изменения сопротивления, вызывая перегрев активной структуры и ухудшение электрических параметров транзисторов.
Пустоты под активной областью изделия в усилителе мощности могут привести к достаточно высокой рабочей температуре, вызывающей, по меньшей мере, нестандартные характеристики выходной мощности, и, возможно, к преждевременному выходу устройства из строя из-за перегрева. Пустоты под областью контактных площадок могут привести к повреждению кристалла на этапе формировании проволочных выводов, под воздействием ультразвуковых колебаний и давления сварочного инструмента.
Для того, чтобы свети к минимуму вероятность возникновения пустот в соединении процесс монтажа необходимо проводить в вакууме или с использованием притирки.
Вакуумная пайка
Различные источники регламентируют максимально допустимое содержание пустот в паяном соединении. Наиболее известная норма — не более 5% от общей̆ площади соединения, при том, что максимальная площадь любой из каверн не превышает 1%. С появлением более мощных и тонких кристаллов многие производители ужесточили требования по наличию пустот до 2% общей̆ площади и менее.
Вопрос о выборе технологии пайки для монтажа мощных кристаллов давно закрыт — ни конвекционная, ни компрессионная, ни парофазная технологии не обеспечивают допустимый процент пустот. В установке вакуумной пайки вакуум, плавно подаваемый̆ непосредственно в момент образования жидкой̆ фазы, практически полностью выводит воздушные каверны из паяного соединения.
Другой отличительной характеристикой данного метода является необходимость использования восстановительной атмосферы смеси азота и водорода для удаления оксидных плёнок и загрязнений с поверхности, препятствующих смачиванию поверхностей, и предотвращения их последующего возникновения в ходе монтажа. Это обусловлено недопустимостью использования флюса в сборках с GaN или GaAs МИС — именно поэтому при монтаже этих устройств используется припой AuSn твёрдой форме.
Третий нюанс, характеризующий данный метод монтажа, предполагает использование специализированной оснастки, фиксирующей преформу и кристалл, как при загрузке изделий, так и в ходе оплавления, когда возможные сдвиги кристалла могут произойти при образовании «мениска» расплавленного припоя.
Достоверно контролировать качество пайки неразрушающим методом можно на установке рентгеновского контроля или с использованием сканирующей акустической микроскопии (Рис. 2), но опыт показывает, что если процесс пайки проведён правильно, то видимые области паяного соединения выглядят блестящими с серебряным оттенком (Рис. 3), в отличие от более тусклого, золотого, который часто является признаком перегрева или завышенной температуры.
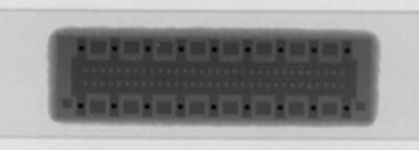
Рис. 2 — Рентгеновское изображение кристалла UMC GH50, смонтированного на эвтектику AuSn в вакуумной печи.
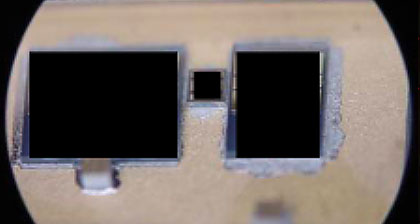
Рис. 3 — Пример качественной пайки транзисторов на эвтектику AuSn (серебряный «мениск» паяного соединения по периметру кристаллов).
Перегрев выше 320°C вреден для МИС GaAs с точки зрения средней наработки до отказа. Например, 30-секундная выдержка транзистора Qorvo (произведённого по технологии 0.25 pHEMT) при 320°C эквивалентна приблизительно 545 часам срока службы при температуре 140°C. В связи с более длительным сроком службы и более высокой температурной устойчивостью устройств GaN, воздействие температур выше 320°C не оказывает столь серьёзного воздействия на среднюю наработку на отказ. Рекомендуемая максимальная температура оплавления для GaAs и GaN МИС производства Qorvo составляет 320°C в течение максимального времени 30 секунд. |
![]() Рис. 4 — пример температурного профиля пайки на эвтектику AuSn. |
Учитывая вышеперечисленные характеристики метода вакуумной пайки оборудование для данного процесса должно отвечать следующим требованиям:
Кондукционный принцип теплопередачи — как нагрев, так и охлаждения изделия должны происходить от контакта последнего с нагретой поверхностью нагревателя. |
![]() Рис. 5 — Инженер-технолог проводит программирование термопрофиля |
Монтаж с притиркой
Альтернативой методу вакуумной пайки при монтаже GaN и GaAs МИС стал метод монтажа с использованием притирки (от scrubbing (англ.) — очистка скребком). Суть метода заключается в использовании механических циклических перемещений кристалла относительно поверхности подложки, подводимых в момент, когда припой находится в жидкой фазе и смачивает обе поверхности (кристалла и подложки) — то есть поверхности «притираются» друг об друга равномерно распределяя слоя припоя под площадью кристалла и обеспечивая его однородность и лучшую адгезию. При этом, особенно важно избежать случайных проскальзываний кристалла, так как их наличие может снизить точность монтажа или нарушить распределение припоя под ним.
В данном методе используется та же эвтектика AuSn, что и при пайке в вакууме, поэтому температурный режим для данных процессов одинаков. Различие состоит в том, что в последнем случае пайка проводится в вакуумной камере, препятствующей свободному рассеянию тепла и, тем самым, поддерживающей равномерность температуры в допустимом диапазоне по всему объёму камеры. В установках монтажа кристаллов данная проблема решается использованием нагреваемого инструмента для монтажа — тепловой фон, создаваемый при его нагреве, выполняет роль барьера для рассеивания тепла и обеспечивает условно равномерное распределение температуры по всему объёму области монтажа. Важно отметить, что в данном случае локальный характер нагрева позволяет свести к минимум тепловое воздействие на соседние, уже установленные, компоненты, обеспечивая более широкое технологическое окно процесса. Для удаления окислов и активации поверхностей также рекомендуется использовать форминг-газ (от англ. forming gas — формовочный газ — смесь азота с водородом с различной молярной долей), хотя, в некоторых случаях допускается использование азота.
Если эвтектический монтаж с притиркой выполнен правильно, то полученное соединение будет отвечать критериям однородности и надёжности, то есть содержать минимальный процент пустот, причем эти характеристики будут выполняться от партии к партии. Типовое значение однородности составляет 99%, при этом средний диаметр пустот не превышает 25 мкм.
Для правильного протекания процесса необходимо управлять многими параметрами: градиент изменения температуры верхнего и нижнего нагревателя, поток газа, усилие монтажа, частота, амплитуда и направление притирки. Таким образом, для реализации данного метода подходит только автоматизированное оборудование, например установка монтажа кристаллов начального уровня FINEPLACER pico ma (рис. 6) или автоматическая система FineXT 5205, обеспечивающая полностью автоматический процесс монтажа в многокристальных СВЧ-модулях. Каждая из этих систем построена по модульному принципу, что позволяет дооснащать установку необходимыми опциями непосредственно в процессе эксплуатации. |
![]() Рис. 6 — Инженер-технолог проводит монтаж кристаллов на эвтектику |
Монтаж кристаллов с применением органического клея
Ещё один распространённый метод монтажа мощных кристаллов на подложки — монтаж с использованием материалов типа адгезив (рис. 7). Адгезив — вещество, обладающее свойством соединять материалы путём поверхностного сцепления. Скрепляющее действие адгезива основано на создании молекулярных связей между ним и поверхностями соединяемых материалов. Очевидно, что адгезивы — это широкий класс веществ, к которым могут быть отнесены как органические клеи типа эпоксидных смол, так и токопроводящие составы типа серебросодержащих паст. Из определения следуют преимущества и недостатки этого метода. С одной стороны, адгезив позволяет компенсировать микронеровности на поверхности, увеличивая площадь контакта, а с другой — взаимодействует с соединяемыми поверхностями только по границе раздела, без взаимной диффузии. |
![]() Рис. 7 — Монтаж кристалла на токопроводящую пасту |
Еще в недавнем прошлом эти органические вещества были рекомендованы для использования только в устройствах с низким энергопотреблением, где не стоит проблема отведения тепла от кристалла. Со временем термические и механические характеристики соединения, образованного адгезивом, приблизились к характеристикам припоя AuSn, а в некоторых случаях и обогнали их. Казалось бы — вот и готовое решение. Но параметры изделия будут зависеть от конечного выходного соотношения ТКР и теплопроводности образовавшегося соединения, а это означает, что рассматривать необходимо систему целиком. Дело в том, что увеличение толщины нанесённого слоя адгезива компенсирует разницу в ТКР кристалла снижая механические нагрузки в процессе термоциклов при эксплуатации, однако снижает и общую теплопроводность соединения. Для компонентов с низким рассеиванием мощности (МШУ, компоненты управления и т. Д.) проблема толщины адгезива не так актуальна, как для транзисторов, когда возможность добиваться тонких (20-40 мкм) и равномерных слоёв токопроводящей пасты является наиболее определяющей в выборе метода монтажа.
Последовательность монтажа при данном методе включает: нанесение материала, цикл захват-совмещение-установка кристалла, полимеризацию. На основании вышесказанного, к самому критичному можно отнести этап нанесения адгезива или пасты на подложку, хотя, конечно, последующие операции требуют не меньшего внимания и времени. Различают несколько методов нанесения, в зависимости от тары, в которой поставляется адгезив, степени автоматизации процесса и типа используемого оборудования, характеристик отпечатка, который нужно получить. Про каждый из этих методов можно написать отдельную статью — остановимся лишь на основных узловых точках, характерных для каждого из методов.
- Дозирование. Используется в автоматическом процессе, как на отдельно стоящих автоматах дозирования (при массовом производстве), так и в качестве модуля на автоматах монтажа кристаллов (при серийном гибком производстве) (Рис.8). Адгезив поставляется в шприцах 3, 5, 10, 30... см3. Метод дает возможность получать рисунки любой геометрии, в основном для средних и больших кристаллов. Погрешность дозы зависит от типа применяемого дозатора. Есть ограничение по вязкости используемых материалов.
- Штемпелевание. Используется как при ручном, так и при автоматическом процессе и реализуется в опциональном модуле установки монтажа кристаллов. Адгезив размазывается тонким слоем в «блюдце» установки. Требует наличия специального инструмента — штемпеля с определённой формой, от которой и зависит геометрия отпечатка. Погрешность дозы зависит от точности изготовления штемпеля и точности оборудования. Используется как для очень мелких, так и для больших кристаллов. Есть ограничение по вязкости используемых материалов.
- Окунание. Используется в основном для ручного процесса при отработке технологии. К преимуществам метода можно отнести универсальность и отсутствие потребности в дополнительных инструментах. Метод менее точен в сравнении с дозированием и штемпелеванием.
- Обратное штемпелевание (технология Finetech). Метод заключается в нанесении на кристалл заранее сформированного отпечатка при помощи специализированного модуля (Рис.9). Реализован в автоматах монтажа кристаллов FineXT 5205 и 6003. Метод отличается высокой скоростью, точностью и повторяемостью.
![]() Рис. 8 — Модуль дозирования |
![]() Рис. 9 — Модуль обратного штемпелевания |
Наиболее распространённый тип адгезива для использования при монтаже мощных МИС — токопроводящая паста, одно- или двухкомпонентная. Так, например, один из лидеров японской промышленности компания KYOCERA в качестве проводящего металла использует в своей однокомпонентной пасте наночастицы серебра. Уникальные характеристики их материала достигаются благодаря технологии nano-Ag, то есть добавлении в состав пасты серебряных частиц субмикронного размера — при спекании эти частицы увеличивают площадь соединения основных частиц материала повышая таким образом теплопроводность соединения до 200 Вт/мК.
Невысокие температуры полимеризации (100–200°С) можно отнести к безусловным плюсам данной технологии — термическое воздействие на сборку сведено к минимуму. Недостатками, помимо уже названных, являются длительное время сушки и невозможность применения высоких температур при последующих сборочных операциях.
Несколько слов о выборе инструмента монтажа
Монтаж кристаллов в корпус или на плату многокристального модуля состоит из следующих итераций — захвата кристалла, позиционирования, установки по месту и присоединения (фиксации). На протяжении этой последовательности действий инструмент находится во взаимодействии с кристаллом — обеспечивает его фиксацию, точность захвата, передачу усилия прижима и тепла.
Исключая совсем уж экзотические случаи, единственно возможный способ фиксации компонента в инструменте — вакуумный захват, при этом контакт кристалла с инструментом происходит либо по граням, либо по лицевой поверхности.
Выбор инструмента основан на следующих критериях:
- Форма и размер кристалла определяют конструкцию инструмента и возможности производителя.
- Топология кристалла — определяет тип захвата.
- Температура процесса задаёт требования к материалу инструмента.
- Прочие требования к механическим и электрическим свойствам материала, типа ESD безопасности, износостойкости, твёрдости и т.д.
- Тип оборудования определяет конструкцию инструмента.
- Стоимость и сроки поставки определяют себестоимость производства.
В каталоге каждого производителя инструментов найдётся не один десяток доступных для заказа серий, однако, как правило, инструмент разрабатывается и изготавливается индивидуально под каждый кристалл с учётом всех вышеназванных критериев (рис. 11). Стоимость и долгий срок поставки не должны в данном случае быть сдерживающим фактором для заказчика — цена ошибки в случае неправильного выбора инструмента будет куда выше.
Основным ограничением при выборе инструмента для монтажа кристаллов МИС является необходимость избегать контакта с лицевой поверхностью кристалла, обусловленная наличие воздушных мостов и других трёхмерных структур на поверхности. Для этих целей наибольшее распространение получили инструменты типа пирамидка. Их конструкция в общем случае предусматривает пирамидальные грани с 2-х или 4-х сторон кристалла и отверстие вакуумного канала (рис. 10). Таким образом, кристалл физически жёстко фиксируется между гранями пирамидки и удерживается вакуумом в процессе монтажа. Автоматизированное оборудование при этом постоянно контролирует уровень вакуума и автоматически определяет был ли правильно определён момент захвата или установки кристалла на поверхность, также оно позволяет аккуратно, плавно воздействовать на кристалл в ходе его подбора или установки, чтобы не повредить хрупкий GaAs, усилия на который, как правило, не должны превышать 40 гр.
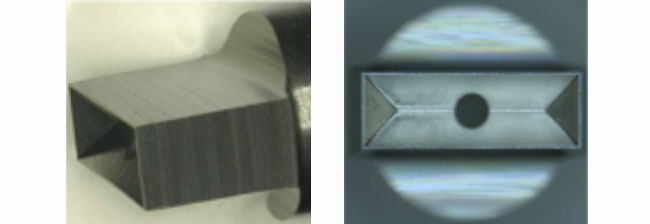
Рис. 10 — Инструмент типа пирамидка с 4-мя гранями.
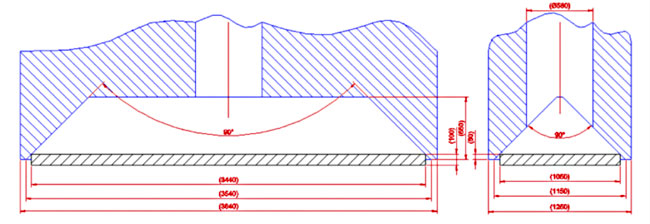
Рис. 11 — Чертёж инструмента типа пирамидка, разработанный под кристалл UMC.
Как обеспечить параллельность при установке длинного компонента типа лазерная линейка? А что делать, если кристалл настолько тонкий (до 50 мкм), что края пирамидки при монтаже контактируют с растекающимся адгезивом или припоем? Решения этих и многих других проблем конечно же существуют и уже давно отработаны на многих предприятиях России. Специалисты Глобал Микроэлектроника ответят на Ваши вопросы и проконсультируют по выбору инструмента.
Общие рекомендации по работе
GaN и GaAs транзисторы и МИСы, как правило, имеют толщину в 50–100 мкм, и габаритные размеры от 800 до 4500 мкм. В большинстве случаев в конструкции присутствуют воздушные мосты. При этом, стоимость кристаллов может превышать 1000 долларов за штуку. Стоимость технологического оборудования участка сборки таких кристаллов даже при самом скромном подсчёте составляет несколько сотен тысяч долларов. Сборки входят в состав наиболее критичных устройств — приёмников и передатчиков современных средств радио- и спутниковой связи, радиолокационных приёмо-передающих модулей и работают на суше, море, воздухе и космосе — там, где отказы недопустимы. Именно поэтому, цена ошибки при неправильном подходе к оснащению производственного участка может дорого обойтись, при чем в репутационном плане гораздо дороже, чем в материальном.
Минимизировать ошибки поможет опыт коллег и партнёров, а также чёткое следование рекомендациям производителя кристаллов по обращению с ними:
Инфраструктура участка. Чистое помещение должно быть правильно спроектировано, построено и аттестовано соответствующими организациями. Требования по содержанию влаги и температуре в помещении определяются стандартами ISO для чистых помещений. Для сборочных операции наиболее оптимальном является класс чистоты 7 по ГОСТ Р ИСО 14644. Должны проводится регулярные проверки на соответствие требованиям.
Основное и вспомогательное оборудование должно быть заземлены, операторы должны носить антистатические браслеты. Тара для хранения и транспортировки также должна быть в антистатическом исполнении, чтобы избежать повреждения дорогостоящего кристалла. Хранить кристаллы необходимо в атмосфере осушенного воздуха в шкафах сухого хранения. Использование азота допускается, но не является обязательным требованием.
Упаковка кристаллов должна обеспечивать сохранность кристалла на всем пути от автомата сортировки и упаковки на полупроводниковой фабрике до тех пор пока он будет подхвачен установкой монтажа кристаллов и не помещён в корпус (подложку). Учитывая сложную конструкцию и повышенную хрупкость GaAs самый удобный вариант упаковки кристалла на среднесерийном производстве — тара Gelpak. Установка монтажа при этом должна обладать специализированным модулем для размещения тары Gelpak с подключением к вакууму для снижения адгезию кристалла и лёгкого отделения от плёнки держателя.
Очистка. Процесс сборки кристаллов подвержен множеству потенциальных осложнений, связанных с загрязнением, целостностью металлизации, состоянием поверхности кристалла и подложки. Загрязнение может происходить из-за образования оксидной плёнки после контакта с атмосферой, попадания органического мусор и пыли из окружающей среды. Такие загрязнения образуют пассивирующий барьер на контактной поверхности, предотвращающий смачивание припоем при оплавлении.
Загрязнения могут быть разделены на физические (механические) и химические. Физические загрязнения держатся на подложке за счёт электростатики — сил Ван-дер-Ваальса, химические — за счёт химических связей с поверхностью заготовки. Физические загрязнения могут быть с лёгкостью удалены множеством методов: от отмывки до нагрева заготовки, при котором молекулы загрязнителя отрываются от поверхности заготовки в ходе теплового движения. Химические загрязнения являются наиболее трудноудаляемыми за счёт прочности связей с поверхностью и могут быть устранены только с помощью химической обработки. Плазменная очистка стала решением для удаления как физических, так и химических загрязнений без применения нагрева и использования жидких сред.
Но даже получив кристалл в надлежащей упаковке и произведя процесс монтажа в точном соответствии с технологией производства, смонтированный кристалл может быть загрязнён, например инструментом для монтажа, не очищенным вовремя — в результате на операцию микросварки кристалл может уйти с загрязнениями на контактных площадках. Таким образом, очистка всех поверхностей, которые соприкасаются с кристаллом, включая инструменты, является обязательной для обеспечения повторяемости процесса.
Входной контроль комплектующих. Качество смачивания и адгезии в процессе эвтектического монтажа кристалла зависит от целостности металлизации подложки. Если золочение имеет низкое качество, недостаточную или неравномерную толщину плёнки, содержит каверны, царапины или отслоения, во время монтажа кристалла могут образоваться пустоты. Показателями качества золочения при наблюдении под оптическим микроскопом является яркий и ровный цвет золота.
Заключение
Процесс монтажа GaN и GaAs кристаллов — важнейшего этапа сборки наиболее критичных устройств широкополосной связи в СВЧ диапазоне, радиолокационных приёмо-передающих модулей последнего поколения, предназначенных для работы на суше, море, воздухе и космосе — заключается в фиксация компонента на носителе (подложке, теплоотводе, пьедестале) с обязательным обеспечением надёжного электрического и термического контакта. В зависимости от типа устройства и условий его эксплуатации реализовать данную технологическую операцию можно различными методами — пайкой в вакууме, монтажом с притиркой, монтажом на адгезив или их комбинацией. Основными ограничительными факторами при разработке технологии — обеспечение теплоотвода, согласование КТР и стоимость.
В связи с активным развитием данного направления в мире и России, в частности, растёт количество предприятий, предлагающих новые разработки, и теперь уже для отечественных фирм быстрый вывод продукта на рынок и снижение себестоимости продукции становится не менее важным, чем достижение требований технического задания заказчика. Развитие современной техники идёт бешеным темпом и времени на раскачку порой просто нет. Если раньше можно было тратить годы на выбор оборудования, гоняясь за новинками по выставкам и пытаясь ухватить «то самое», чего ни у кого ещё нет, то теперь нужно действовать решительно, опираясь в большей степени на опыт зарубежных коллег и партнёров, уже прошедших этот этап. Ошибок не этом пути не избежать, но российским специалистам, осваивающим новые технологии, не стоит этого опасаться, ведь «лучший способ заглянуть в будущее — это создать его».
Использованные источники:
1. Qorvo, «GaAs and GaN Die Assembly and Handling Procedures»
2. SemiGen, «Eutectic Die-Attach of GaN and GaAs MMICs»
3. UMC, «Application note for GaN on SiC Transistor»
4. Northrop Grumman, «GaN IC Die Handling, Assembly and Testing Techniques»
5. Randy Hamm, Ken Peterson, «Maintaining Low Voiding Solder Die Attach for Power Die While Minimizing Die Tilt», 2015
6. И. Корочкин, В. Хриченко «Три кита плазменной очистки», 2017.
7. Источник фото #6: АО «Институт Микроволновых Интегральных Систем» («Микро-ВИС»)
8. Источник фото #7: компания F&S Bondtec
9. Источник фото #8 и #9: компания Finetech
10. Источник фото #10 и #11: UMC.